I finally got around to doing a wallpaper using my chilli motif using potatoe's as the block print and fabric paint on calico. a very enjoyable task with good results.
Wednesday, 16 February 2011
Wednesday, 9 February 2011
HOT HOT CHILLI











Tuesday, 8 February 2011
printing machines



history of the digital printing
As little as 15 years ago digital printing of textiles, compared with paper for the relatively benign office environment, no doubt looked like mission impossible. The demands of the textile application are extreme. Among them:
It is still clearly new territory, but we’ve progressed beyond curiosity seekers, says I.T. Strategies. Printer and textile manufacturers know that this new opportunity is important to their companies. It’s a new frontier, it’s something like the old Wild West. Some of the energy is from the existing textile industry. Some from outside, like Colorlab, Ltd. That’s the color processor in Providence, RI, who decided to refocus his business entirely on fabric printing. Their new company name is Practical Imaging. (See detailed case below.)
Another thing new is the much wider variety of fabrics that can now be digitally printed: silks, polyester, car seats, cotton. Actually, now almost everything can be printed. It’s something like the development of digital presses. At first they required a narrow selection of closely controlled papers. Now they are much more flexible. Textiles is already going this way. But each of these materials has its own ink requirements.
And another problem is getting the ink to go through all the fiber. There are silk scarfs and car seats. And nonwovens such as Tyvek®--incredibly different requirements. Indeed, inks are a major frontier and a number of ink companies want to know more.
Other important issues include mass customization and how to deal with the reality that there need to be integrated solutions involving a sequence of operations such as pre-treating, printing, finishing, cutting and sewing. This poses a contradiction: digital printing opens the door for on-demand and decentralized manufacture. But how do you deal with these pre- and post-printing requirements in an office or other decentralized environment? One long-term market trend, for example, includes the movement of textiles and apparel manufacturing to SE Asia. Less than 5% of the world’s textile printing production was said to still be in North America. And there are some negative fashion trends, such as increasing preference toward single colors rather than printed patterns. Will digital printing offset or accommodate such trends?
- more than a half dozen common types of synthetic and natural fibres, each with its own ink compatibility characteristics;
- dealing with a stretchable, flexible, often highly porous and textured surface;
- extreme use requirements including light, water fastness (sweat, too) through finishing operations and often outdoor use, heavy wear, abrasion, and cleaning;
- for some apparel applications, challenging registration requirements since separate pieces need to be assembled;
- not just sight, but also touch requirement;
- much greater absorbancy, requiring many times the ink volume compared with printing on papers.
It is still clearly new territory, but we’ve progressed beyond curiosity seekers, says I.T. Strategies. Printer and textile manufacturers know that this new opportunity is important to their companies. It’s a new frontier, it’s something like the old Wild West. Some of the energy is from the existing textile industry. Some from outside, like Colorlab, Ltd. That’s the color processor in Providence, RI, who decided to refocus his business entirely on fabric printing. Their new company name is Practical Imaging. (See detailed case below.)
Another thing new is the much wider variety of fabrics that can now be digitally printed: silks, polyester, car seats, cotton. Actually, now almost everything can be printed. It’s something like the development of digital presses. At first they required a narrow selection of closely controlled papers. Now they are much more flexible. Textiles is already going this way. But each of these materials has its own ink requirements.
And another problem is getting the ink to go through all the fiber. There are silk scarfs and car seats. And nonwovens such as Tyvek®--incredibly different requirements. Indeed, inks are a major frontier and a number of ink companies want to know more.
Other important issues include mass customization and how to deal with the reality that there need to be integrated solutions involving a sequence of operations such as pre-treating, printing, finishing, cutting and sewing. This poses a contradiction: digital printing opens the door for on-demand and decentralized manufacture. But how do you deal with these pre- and post-printing requirements in an office or other decentralized environment? One long-term market trend, for example, includes the movement of textiles and apparel manufacturing to SE Asia. Less than 5% of the world’s textile printing production was said to still be in North America. And there are some negative fashion trends, such as increasing preference toward single colors rather than printed patterns. Will digital printing offset or accommodate such trends?
textile printing, digital printing methods
-- Textile Printing The application of color to a fabric in a design or pattern (localized dyeing) Modern printing generally incorporates one of the following techniques: Flat-bed screen printing Rotary screen printing Engraved roller printing - Heat transfer printing.
digital printing
In this form of printing micro-sized droplets of dye are placed onto the fabric through an inkjet printhead. The print system software interprets the data supplied by a cademic_Textiledigital image file. The digital image file has the data to control the droplet output so that the image quality and color control may be achieved. This is the latest development in textile printing and is expanding very fast. Digital Textile Printing
digital printing
In this form of printing micro-sized droplets of dye are placed onto the fabric through an inkjet printhead. The print system software interprets the data supplied by a cademic_Textiledigital image file. The digital image file has the data to control the droplet output so that the image quality and color control may be achieved. This is the latest development in textile printing and is expanding very fast. Digital Textile Printing
technical advances in textiles
The rapidly evolving world of digitally printed textiles is a reflection of several unique and contrasting business models that create challenges, threats and opportunities to the future of the textile printing market.
The traditional textile industry looks at it from their traditional mass production business models and complains it is too slow and too expensive relative to the conventional screen printing technologies most commonly used in the market today. For these companies, digital textile printing has proven to be a tremendous cost savings in sampling only, while moving to conventional methods for their mass production needs.
With textile seminars and exhibits being presented on in increasingly frequent basis at wide format printing and graphics trade shows, it is apparent that other industries are looking at this technology with an eye towards what it can do, as opposed to what it can't do. Since these industries already support short run and customization business models as a reflection of their technology driven businesses, textiles simply represent a new market to which they can sell their excellent command of printing technology as well as their ability to produce short run production with quick turn around - a business practice that is foreign to the conventional printing industry as a result of the analog technology on which it is founded.
So, is the wide format printing industry a threat to the conventional textile printing industry? Yes and no. If the textile industry waits for the technology to evolove in order to adopt it as a production tool, then yes, they will have lost many opportunities to new players. If, on the other hand, they can re-engineer their businesses to support the growing consumer demand for customized product, then they can lessen the probability of market errosion.
The wide format printers are not without their challenges to the new market opportunities. While most have mastered the basics of printing on paper, vinyl and even plastics, printing on textiles that vary in fiber content, weight, thickness, ink absorbency, and yarn size, that must be washable, light fast, crock resistant and wearable and require multiple ink sets can present a whole new set of challenges, if not at least a learning curve. Satisfying a textile industry that is accustomed to the color accuracy that spot color offers is yet another challenge.
With an eye towards the growing number of wide format printers, graphic artists and entrepreneurs that see the market opportunities, we offer a primer in digital textile printing
The traditional textile industry looks at it from their traditional mass production business models and complains it is too slow and too expensive relative to the conventional screen printing technologies most commonly used in the market today. For these companies, digital textile printing has proven to be a tremendous cost savings in sampling only, while moving to conventional methods for their mass production needs.
With textile seminars and exhibits being presented on in increasingly frequent basis at wide format printing and graphics trade shows, it is apparent that other industries are looking at this technology with an eye towards what it can do, as opposed to what it can't do. Since these industries already support short run and customization business models as a reflection of their technology driven businesses, textiles simply represent a new market to which they can sell their excellent command of printing technology as well as their ability to produce short run production with quick turn around - a business practice that is foreign to the conventional printing industry as a result of the analog technology on which it is founded.
So, is the wide format printing industry a threat to the conventional textile printing industry? Yes and no. If the textile industry waits for the technology to evolove in order to adopt it as a production tool, then yes, they will have lost many opportunities to new players. If, on the other hand, they can re-engineer their businesses to support the growing consumer demand for customized product, then they can lessen the probability of market errosion.
The wide format printers are not without their challenges to the new market opportunities. While most have mastered the basics of printing on paper, vinyl and even plastics, printing on textiles that vary in fiber content, weight, thickness, ink absorbency, and yarn size, that must be washable, light fast, crock resistant and wearable and require multiple ink sets can present a whole new set of challenges, if not at least a learning curve. Satisfying a textile industry that is accustomed to the color accuracy that spot color offers is yet another challenge.
With an eye towards the growing number of wide format printers, graphic artists and entrepreneurs that see the market opportunities, we offer a primer in digital textile printing
handprinting


Recent excavations of the Red Sea ports have also brought out a greater range of printed textiles. These date back to 800 AD. Their technique and design point to a western Indian origin. The printing industry has its important centres all over India. The most important cotton printing centres that follow the traditional technique of printing are found in the desert belt. The important centres of hand printing in Rajasthan are Jaipur, Sanganer, Bagroo, Pali and Barmer.
Various printing techniques have been developed including, direct printing, resist printing, and screen-printing. Direct printing is practiced all over India where a bleached cotton or silk fabric is printed with the help of wooden blocks, with beautifully carved designs. But first the outline block is printed, after which the blocks for filling in the colors are to be utilized. If the background is to be a light color, the cloth is dyed after the printing has been completed. Normally, three to four colors are used.
In the resist technique, a paste made up of different material is used over areas to be printed which are required to resist the dye. The fabric is then immersed in the dye bath. In some cases, clay mixed with resin is used for printing areas which have to be protected from the dye; in others hot wax is used. After dying, the fabric is washed in flowing water or in hot water to melt the wax. Some of the dark color of the background material flows on the protected area, thus creating a soft tonal effect.
The batik technique is a development from this form of resist printing. Here the fabric is painted with molten wax and then dyed in cold dyes after which the cloth is washed in hot water. This results in the melting of the wax and emergence of the patterned cloth. The effect of the resist technique in printing is soft and subdued and the outlines are not so clearly defined as in the case of the painted batik.
.
lithography,letterpress
Hand printing techniques used by artists are as follows:
Planographic Printing
Lithography is derived from the Greek word meaning to write on stone. Aloys Senefelder invented lithography in 1798. Unlike the techniques listed below the printed and non-printed areas share the same surface. Lithography works on the principle of grease repelling water and adhering to ink. Thus the materials that the artists uses to make their image with are "greasy" and these are the areas that will pick up the ink from the roller. The rest of the plate or stone surface is covered with a thin film of water, which serves to repel the ink during printing. In this way the drawn area of the print is what is transferred to paper.
Letterpress
is a printing technique that actually embeds the artwork into the paper. The softer the paper is, the deeper the inked plates sink the image into the surface, creating a textured, 3 dimensional design. The technique of letterpress printing began in the mid 1400s with the invention of movable type by Johannes Gutenberg. For centuries, letterpress was the only method of printing used for reproduction. Letterpress printing is a very labour-intensive process. The press operator handsets and hand inks the metal plates that are used to imprint the designs and lettering onto the paper. The process of letterpress printing is not only extraordinarily time consuming, but also is a tedious craft that requires the utmost attention to detail. Today, after centuries of change and technological advances in printing methods, the processes and craft of letterpress printing have remained virtually unchanged.
or many artists lithography appeals most to them as artists as it is very similar to drawing and painting as one uses pencils and brushes which are prepared specifically for lithography. The artist works directly onto the grained limestone, grained film or aluminium plate. Various abrasives are used in the graining process so that a variety of either smooth or rougher surfaces can be worked on depending on the preferences of the artist concerned.
Each colour used on a lithograph requires a separate plate/film or stone to be used and the artist has to make the colour separations themselves. The complicated technical nature of lithography takes time and knowledge to do effectively and usually requires that the artist collaborates with a skilled masterprinter.
Planographic Printing
Lithography is derived from the Greek word meaning to write on stone. Aloys Senefelder invented lithography in 1798. Unlike the techniques listed below the printed and non-printed areas share the same surface. Lithography works on the principle of grease repelling water and adhering to ink. Thus the materials that the artists uses to make their image with are "greasy" and these are the areas that will pick up the ink from the roller. The rest of the plate or stone surface is covered with a thin film of water, which serves to repel the ink during printing. In this way the drawn area of the print is what is transferred to paper.
Letterpress
is a printing technique that actually embeds the artwork into the paper. The softer the paper is, the deeper the inked plates sink the image into the surface, creating a textured, 3 dimensional design. The technique of letterpress printing began in the mid 1400s with the invention of movable type by Johannes Gutenberg. For centuries, letterpress was the only method of printing used for reproduction. Letterpress printing is a very labour-intensive process. The press operator handsets and hand inks the metal plates that are used to imprint the designs and lettering onto the paper. The process of letterpress printing is not only extraordinarily time consuming, but also is a tedious craft that requires the utmost attention to detail. Today, after centuries of change and technological advances in printing methods, the processes and craft of letterpress printing have remained virtually unchanged.
or many artists lithography appeals most to them as artists as it is very similar to drawing and painting as one uses pencils and brushes which are prepared specifically for lithography. The artist works directly onto the grained limestone, grained film or aluminium plate. Various abrasives are used in the graining process so that a variety of either smooth or rougher surfaces can be worked on depending on the preferences of the artist concerned.
Each colour used on a lithograph requires a separate plate/film or stone to be used and the artist has to make the colour separations themselves. The complicated technical nature of lithography takes time and knowledge to do effectively and usually requires that the artist collaborates with a skilled masterprinter.
Tuesday, 1 February 2011
shoes and clotheing with repeating pattern



HENNIE HAWORTH DESIGNER
I think the bottom print is really sweet with all the differnt cup cakes it would look nice in a girlie kitchen.the artist is Hennie haworth,website hennie hawworth
.repeating patterns.co i like the

complex patterns on this print ,and how every shape was different ,hennie hayworth is also a
freelance illustrator that lives and works in London. Having studied illustration at Brighton University her client list which includes:

manmade repeating patterns


1606 reapeating patterns
There are 1606 repeating patterns which implies that further choices must be made.
These can be conveniently divided into five further groups according to the type of rotations in the pattern. A repeat pattern can have rotations of order 6, 4, 3, 2 or none.
For rotations of order 6 an example is:
(Note the point with six shapes meeting at a point - there are also other point with rotations of order 3.)
For rotations of order 4 an example is:
For rotations of order 3 an example is:
For rotations of order 2 an example is:
For a pattern with no rotations an example is:
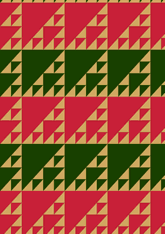
These can be conveniently divided into five further groups according to the type of rotations in the pattern. A repeat pattern can have rotations of order 6, 4, 3, 2 or none.
For rotations of order 6 an example is:
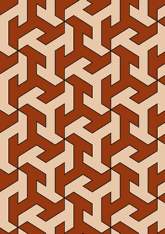
For rotations of order 4 an example is:
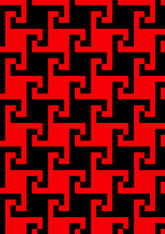
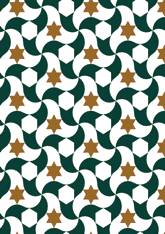
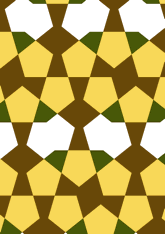
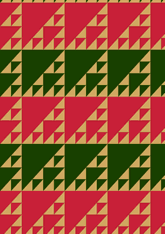
Subscribe to:
Posts (Atom)